Complete Machining and Integration of Functions in Grinding
The INDEX Group practices versatility — not only in its own products, but also in their manufacture. Grinding machines from Glauchau play an important role in this process.
The INDEX plants in Esslingen are one of the largest machine tool manufacturers in the world. An important ingredient in the recipe for success is the constant search for improvement opportunities. And least of all does this stop at the company’s own processes.
A mastermind when it comes to manufacturing efficiency at INDEX is site production manager Martin Steiner: “Our customers require special solutions and this results in special machine components. Thus the central question is: how can we meet the special requirements of these components, which are often only realized in small runs, as economically as possible?“ Martin Steiner also has the answer at hand: “Due to the INDEX philosophy of providing customers with complete machining with our machines, we have long been sensitized to the potential of function integration. We know the advantages and of course use them ourselves every day. By constantly questioning existing manufacturing processes, new solutions are regularly created.“
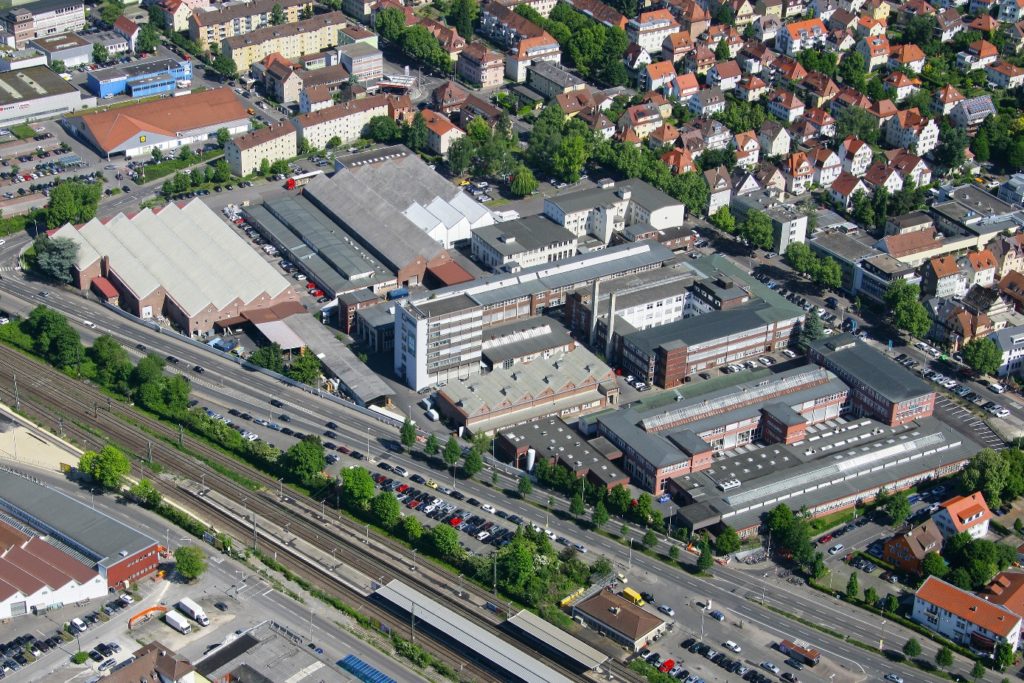
WEMA Glauchau scores with universal machining
Universality is the keyword when it comes to equipping the Esslingen manufacturing facility. This criteria is also important when purchasing a machine for quill production. Therefore, Martin Steiner turned to Werkzeugmaschinenfabrik (WEMA) Glauchau, a company whose grinding machining center (SBZ) WOTAN® S6 U INDEX has already owned and operated successfully.
“When you have a good partner, you naturally ask them for a solution first. Of course, you also look around at other manufacturers. But the way we needed it, no one else would have implemented it for us. Universal machining is really a big advantage of WEMA, making it the only manufacturer that has implemented internal and external grinding with two separately operating grinding units.“
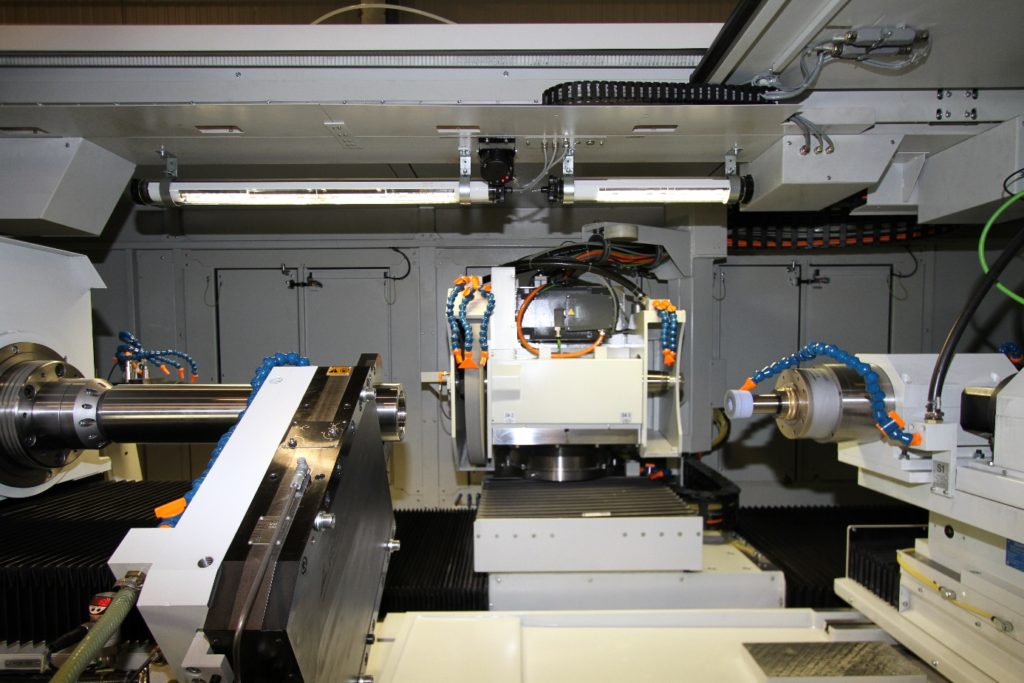
Increased efficiency through automatic mold change & modern sensor technology
“The batch sizes for the production of quills are between 2 and 100 pieces. Considerable time is spent on retooling,“ says Martin Steiner. A new system was needed to significantly increase these setup times and the processing spectrum compared to the older grinding center, with the goal of relieving bottleneck machines upstream and downstream through process integration, significantly reducing flow times in-house, and creating a low-manpower operation.
The machine concept of the WOTAN® S6 U was expanded to include a tool changer for this purpose. “For us, the integration of an automatic tool changer was a completely new challenge,“ recalls Ronald Krippendorf, Managing Director of WEMA. Transfer positions had to be defined and a breakage sensor system integrated. After all, the machine was supposed to automatically detect tool breakage and replace the affected tool on its own.
However, not just any system was attached, but a tool change system that is already in use in series on INDEX machines. Last but not least, a series HSK-A63 motor spindle manufactured by INDEX also had to be integrated for the tool change. “All in all, a complex but very instructive task.“
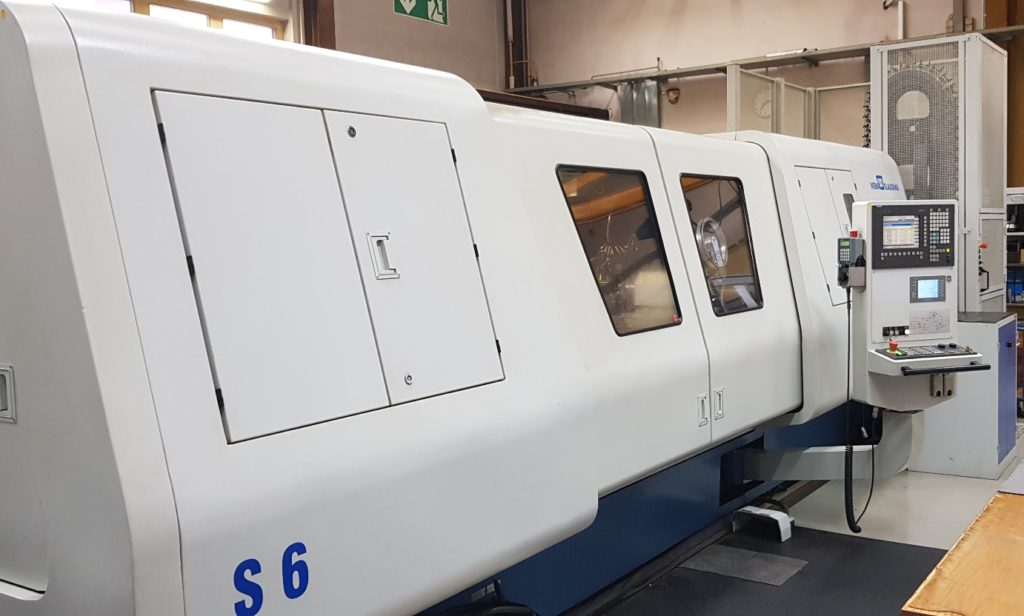
Significantly reduced flow times
The machine is equipped with an independently operating internal grinding unit, which is equipped with three motor spindles and a tailstock, and an external grinding unit on which three external grinding wheels are positioned. INDEX specified the use of a self-centering guide steady rest as well as a special clamping technology, so that the concept of 5‑sided complete machining could be implemented. The new WOTAN® S6 U grinding center thus allows comprehensive quill and spindle machining (internal, external and face machining). For the dressing units for internal and external grinding, the holders were manufactured by INDEX, and this INDEX quick-change system (W‑gearing) was integrated into the WEMA WOTAN® S6 U upon request. The tool changer provides more than 80 tools for drilling, milling, grinding, measuring, and other operations on the quill front. With this immense flexibility, the workpieces are completely machined on one machine and do not have to be distributed among several machines. In addition to shortening changeover times, this also reduces laydown times and flow times within production. Previously, laydown times of three to eight days were incurred per batch during the subsequent operation. With the complete machining, “the subsequent operation has been completely integrated to 100% and a shift between different workshops has been eliminated“ says Steiner.
Process-reliable and high-precision grinding machining
Another major advantage of WEMA is the process reliability of the grinding machining center. “With our quantities, i.e. batch sizes between 2 and 100 pieces, we do have 1–2 minutes longer machining times, but in return we have a lower-manpower- or nearly unmanned process. The important thing here is that the process reliability is very high. When machining quills, we measure the tolerances of the fitting holes once a day. At the beginning of working with the new machine, we measured every part but quickly realized: The WOTAN® does the job! The process is stable! The machine holds the tolerance all day long!“ describes Steiner.
High-precision workpiece clamping and complete machining also enable the machine to achieve previously unattainable accuracies, such as cylindrical form deviations of less than 3 µm over a length of 1300 mm, dimensional tolerances of ± 1 µm, and concentricity deviations between inner bores and lateral surfaces of less than 1 µm.
Due to these consistently high accuracies in conjunction with an automated and autonomous process with enormously high process reliability, the required operator input is also tremendously reduced. The operator capacity that is freed up can therefore be used in parallel for other machining operations on other machines.
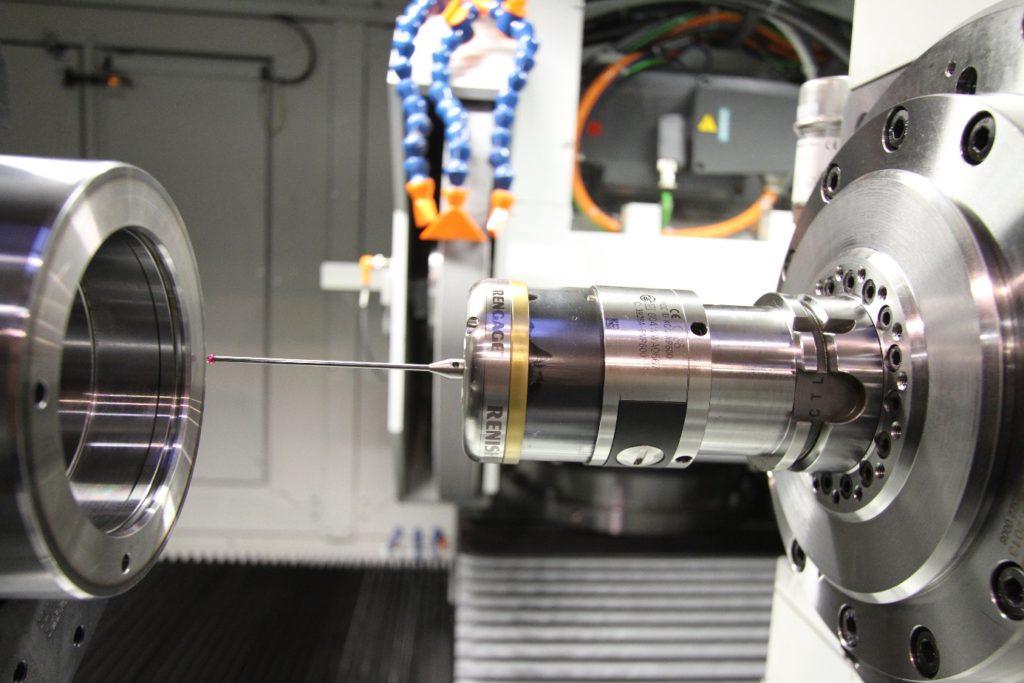
On the road to success with customized solutions
Above all, the requirements for an increase in precision, which INDEX had set as a goal at the beginning of the project, could thus be clearly exceeded. Martin Steiner is convinced: “For such and similar tasks, we would definitely turn to WEMA again. What the Glauchau-based company delivers technically is a real specialty.“
The response that WEMA is receiving from other customers to the offering of its WOTAN® S6 U grinding machining center clearly indicates that the market needs this concept. Meanwhile, the WOTAN® S3 U is also available with a smaller, fully integrated tool changer with five slots. This means that three external and seven internal machining tools are available in just one machine for users with a more specialized machining spectrum.
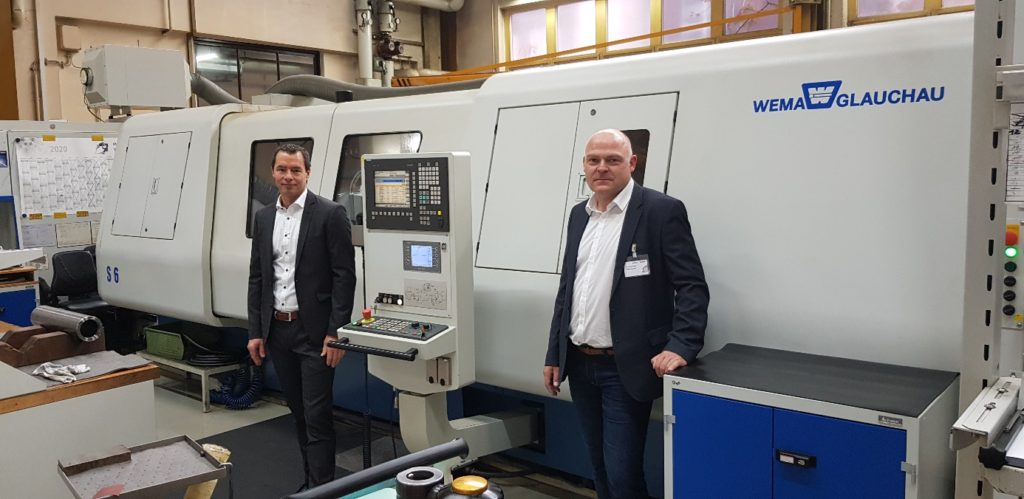
Facts about the WOTAN® S6 U grinding machining center from WEMA Glauchau
- Complete machining in one clamping
- Automatic tool change system with 80 seats
- Machining with geometrically determinate and indeterminate cutting edge
- Machining of chuck and shaft shaped parts (steady rest guided)
- Machining of shaft-shaped parts between centers (tailstock on B2 axis)
- Cylinders, cones, polygons, threads, eccentrics, grooves, and much more
- Three internal grinding spindles (on B2 axis), one of which includes an automatic clamping interface
- Three external grinding tools (fixed on B3 axis)
- External grinding wheels with a maximum diameter of 600 mm
- Power chuck (mandrel)
- Automatic self-centering bezel
- Automatic transfer of components between peak voltage in steady rest voltage
Options
- Innenrundtisch mit bis zu 4 Innenschleifspindeln und einen Reitstock
- wechselseitiger Einsatz von riemengetriebenen Innenschleifspindeln und Motorspindeln
- feststehende Außenschleifeinheit mit einer Schleifscheibe (30°, 45° oder 90° zur Werkstückachse) oder
- hydrostatische Werkstückspindel
- Taster zur Nullpunktmessung
- feststehende und/ oder angetriebene Abrichtwerkzeuge
- In- und Post-Prozess-Messinstrumente
- Internal rotary table with up to four internal grinding spindles and a tailstock
- Alternating use of belt-driven internal grinding spindles and motor spindles
- Fixed external grinding unit with one grinding wheel (30°, 45°, or 90° to the workpiece axis) or hydrostatic workpiece spindle
- Probe for zero point measurement
- Fixed and/or driven dressing tools
- In-process and post-process measurement tools
About Werkzeugmaschinenfabrik (WEMA) Glauchau
WEMA GLAUCHAU GmbH is a medium-sized Saxon mechanical engineering company whose roots go back to the year 1883. Grinding machines of the highest quality and precision, of which over 10,000 have been sold worldwide to date, are the company’s strengths. WEMA GLAUCHAU offers machines, technologies, and services from a single source, and is part of the internationally operating NILES-SIMMONS-HEGENSCHEIDT Group.
About the holding company NILES-SIMMONS-HEGENSCHEIDT GmbH
The NILES-SIMMONS-HEGENSCHEIDT Group (NSH) focuses its business activities on research, development, manufacturing, and sales of machine tools with the aim of producing products of the highest quality, innovation, and energy efficiency. NSH Group is one of the 30 largest machine tool manufacturers in the world and operates in five industries: Engineering, Automotive and Truck, Aerospace, Railway and Metro, and Tool and Die.
About INDEX-Werke GmbH & Co KG Hahn & Tessky
With its brands INDEX and TRAUB, the INDEX Group is today one of the world’s leading manufacturers of CNC lathes. With six production sites and six international sales and service companies as well as a broad dealer network, the Esslingen-based group of companies is present at 80 locations worldwide.
Contact
Ronald Krippendorf
Ronald Krippendorf · Managing Director
Werkzeugmaschinenfabrik (WEMA) Glauchau
+49 3763 61–100
r.krippendorf@nshgroup.com
Rainer Gondek
Head of Marketing INDEX-Werke GmbH & Co KG Hahn & Tessky